As seis grandes perdas da produção é uma perspectiva sobre o tempo de produção perdido nos equipamentos. Da mesma forma que o OEE, as seis grandes perdas tem origem no TPM (Manutenção Produtiva Total). Na verdade, um dos objetivos do TPM é eliminar as seis grandes perdas.
Um dos caminhos mais eficazes para melhorar o OEE é por meio das seis grandes perdas de produção. Vamos passar algum tempo explorando maneiras de alavancar essa ferramenta como parte de seu programa de melhoria.
Então, quando aplicamos métodos e ferramentas para otimização de recursos e redução de desperdícios na empresa caminhamos na direção do conceito de six big losses.
O que é six big losses (seis grandes perdas)?
O conceito de abordagem de erro é uma metodologia aplicada visando identificar as verdadeiras causas de perdas de um processo fabril.
Primeiros benefícios
Conhecer as perdas direcionam os colaboradores na identificação e eliminação dos erros que as causaram.
As falhas
A falha é um evento adverso negativo que pode interromper o processo de maneira parcial ou integral, temporariamente ou definitivamente. Existem vários tipos de falhas, desde equipamentos a falhas de processos.
Quando falamos em falha de recursos, estamos avaliando a disponibilidade desses recursos. A disponibilidade é o grau pelo qual a operação está preparada para funcionar. Uma operação não está disponível se falhou ou se está sendo reparada após uma falha.
Causas comuns
Dentre as causas mais comuns de falhas, podemos citar a falha de ferramentas, quebras e manutenção não planejada. Outros motivos comuns não incluem operadores ou materiais como bloqueios externos que não comprometem a disponibilidade total da máquina.
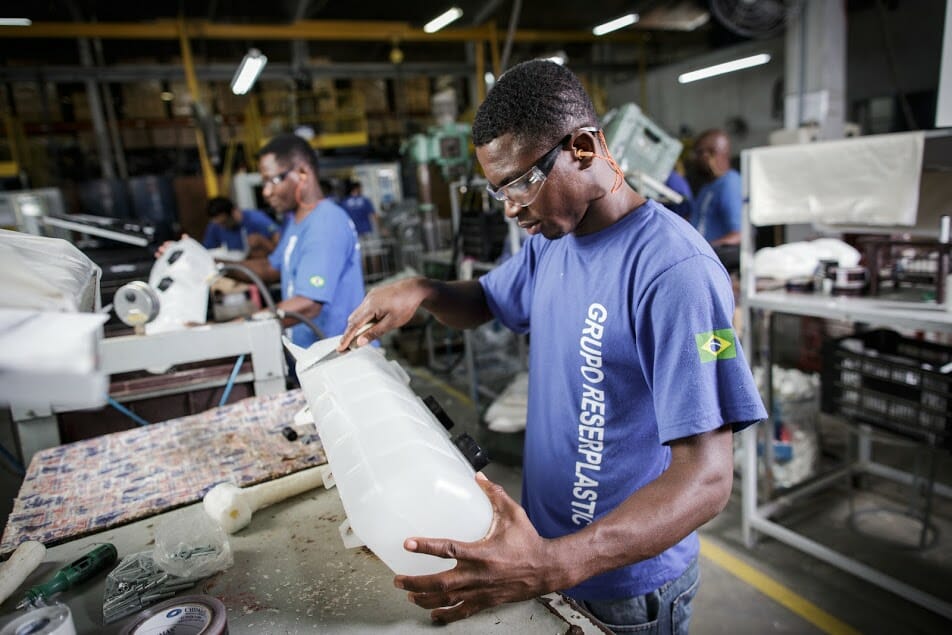
As seis grandes perdas
1ª perda: Por quebra devido a falhas
A indisponibilidade do recurso se dá no momento em que uma determinada atividade não planejada interrompe o fluxo no sistema produtivo, neste caso, incluem-se, quebras e falhas de suprimentos e equipamentos.
2ª perda: Por tempo de SETUP
O tempo de preparação de máquinas e equipamentos influencia no sistema produtivo à medida que ocorrem as alterações na preparação ou mudança dos recursos produtivos. É um evento como umatroca de ferramentas, matrizes ou equipamentos, além de aguardar materiais, peças ou pessoas da equipe.
3ª perda: Por pequenas paradas e operação em vazio
É uma perda de velocidade que ocorre por um curto período. Pode ser causada por bloqueios, acúmulos, limpeza e inspeção.
4ª perda: Por redução da velocidade de operação
A redução de velocidade ocorre pelo mau funcionamento do recurso. Geralmente, as causas podem ser: falta de manutenção, desgaste e configurações inadequadas aplicadas à máquina.
5ª perda: Rejeição de Inicialização
Máquinas recém-instaladas, equipes se adaptando aos novos recursos ou início de produção numa máquina, podem gerar perdas de produção. Definir os parâmetros adequados para iniciar uma produção, testes com menores quantidades podem impactar positivamente no ciclo de produção gerando melhora no desempenho dos equipamentos e na qualidade do produto ao mesmo tempo.
6ª perda: Rejeição de Produção
Esses defeitos são classificados como perda de qualidade. O acompanhamento de não conformidade da produção permite entender a falha ocorrida. Nesse caso há perda de materiais e mão de obra aplicada, havendo a necessidade de retrabalho e até mesmo descarte do produto. O que consome mais tempo dos recursos disponíveis para refazer o que já foi feito.
O que percebemos?!
Conhecer as seis grandes perdas ajuda a manter a qualidade, velocidade e otimização do sistema produtivo. Para melhorar os resultados da produção é necessário o envolvimento de toda a equipe de produção na identificação de erros e para possíveis correções e melhorias.